AUTOMATION
Our Automation Division team has thirty three years of efforts into outperforming our own best in every aspect of the services we provide to our customers. Development of control systems solutions, EPLAN and AutoCAD electrical project design, development of PLC/PAC and HMI/SCADA software applications, panel building, IEC/UL/CSA certification, customer support and beyond, all are performed in accordance with rigorous internal procedures and standards, typically stricter than the customer requirements.
TERI’s production facility at the Tax-Free Zone Pirot has a proven track record of producing high quality systems certified in accordance with IEC, UL and CSA requirements and exported to EU, USA, Canada, and Mexico to the great satisfaction of the end users. As of year 2023 the Panel Building Shop is UL certified for manufacturing of Industrial Control Panels for USA and Canada. Product iQ | Search (ulprospector.com)
Our Automation Division main partners are Rockwell Automation and KUKA. TERI Engineering is Rockwell Automation Gold System Integrator.
The division’s relatively new activity is Design-To-Order and Manufacture-To-Order of complete machines in partnership with regionally established OEMs. A large portion of our production is exported worldwide.
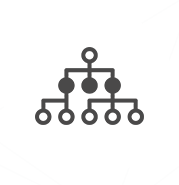
Our Automation Division team has thirty three years of efforts into outperforming our own best in every aspect of the services we provide to our customers. Development of control systems solutions, EPLAN and AutoCAD electrical project design, development of PLC/PAC and HMI/SCADA software applications, panel building, IEC/UL/CSA certification, customer support and beyond, all are performed in accordance with rigorous internal procedures and standards, typically stricter than the customer requirements.
TERI’s production facility at the Tax-Free Zone Pirot has a proven track record of producing high quality systems certified in accordance with IEC, UL and CSA requirements and exported to EU, USA, Canada, and Mexico to the great satisfaction of the end users. As of year 2023 the Panel Building Shop is UL certified for manufacturing of Industrial Control Panels for USA and Canada. <a href=”http://ulprospector.com”>Product iQ | Search (ulprospector.com)</a>
<img class=” wp-image-979 aligncenter” src=”https://terieng.co.rs/wp-content/uploads/2023/12/cuslistv.png” alt=”” width=”65″ height=”53″ />
Our Automation Division main partners are Rockwell Automation and KUKA. TERI Engineering is Rockwell Automation Gold System Integrator.
<img class=”wp-image-981 aligncenter” src=”https://terieng.co.rs/wp-content/uploads/2023/12/ra.png” alt=”” width=”210″ height=”78″ />The division’s relatively new activity is Design-To-Order and Manufacture-To-Order of complete machines in partnership with regionally established OEMs. A large portion of our production is exported worldwide.<span id=”more-225″></span>
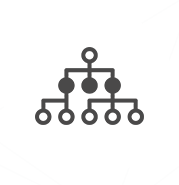
- INDUSTRIAL AUTOMATION AND CONTROL
- THE CONNECTED ENTERPRISE
- ROBOT SYSTEMS
INDUSTRIAL AUTOMATION AND CONTROL
The rapid evolution of technology in industrial automation systems requires tighter integration between devices on the plant floor and the rest of the enterprise. This involves a secure network infrastructure, smart devices for efficient data collection, and the ability to turn data into actionable information.
The integration of control and information across the enterprise enables our customers to optimize their operations by connecting the plant, site, facility, and people. We deliver industrial automation and control through our control systems, motor control, and smart devices portfolios. The combination of these three platforms are architected and designed to help you build the most efficient industrial automation system to meet your needs.
Integrated Architecture
Integrated control systems facilitate smart manufacturing for your industrial automation solution. Rockwell Automation Integrated Architecture® system enables the deployment of an industrial control system individually at a machine- or line-level to solve specific needs. It can then be scaled across multiple lines or plants to achieve enterprise-wide business objectives. It helps converge control and information to deliver the connected enterprise with smarter technology, enhanced productivity, and a more secure environment. The Integrated Architecture portfolio includes ControlLogix control, FactoryTalk visualization, Kinetix motion, and Cisco-based Stratix networking solutions. Our everyday experience from various projects is that this technology has the power to improve plant processes at every stage of manufacturing, from design and installation to operation and maintenance.
Intelligent Motor Control
Efficient motors drive performance and the impact of motor failure can be significant. With intelligent motor control devices, our clients can improve productivity and help avoid motor failures with an integrated, data-driven approach. The Allen-Bradley portfolios of PowerFlex® variable frequency drives, Kinetix® servo drives and CENTERLINE® motor control centers offer solutions for any application with requirements for speed, torque or positioning control. To gain further advantages we ensure that they are combined with the Logix control architecture to reduce the design time, keep clients connected to the operations and help them to be more productive.
Universal Automation System Designer
The Rockwell Automation Studio 5000® environment combines engineering and design elements into one standard framework that enables optimized productivity and reduced commissioning time. The Studio 5000 is a universal system designer that covers of stages of one complex project: Architect, Logix Designer, View Designer, Application Code Manager and Logix Emulate.
https://www.rockwellautomation.com/en-us/products/software/factorytalk/designsuite/studio-5000.html
Industrial Networks
For plants to become information driven, they need a strong foundation consisting of one industrial network architecture. It is crucial to send data to the right place, at the right time, and in the right context. A network infrastructure that is built on standard Ethernet and IP enables the flow of data across your global enterprise. Industry adoption of EtherNet/IP™ for control and information enables the convergence of industrial and enterprise networks. To support and accelerate this network convergence, Rockwell Automation has collaborated with Cisco and other partners to provide design guidance and best practices to deploy scalable, robust, secure, safe, and future-ready industrial network architectures. They have addressed topics relevant to both operations technology (OT) and information technology (IT) professionals. Rockwell Automation offer of industrial network products consists of a wide variety of industrial network solutions including switches, routers, physical media, and connecting products.
Industrial Automation Components
We offer a portfolio of Allen-Bradley industrial control products that deliver proven and predictable performance over the full life of the product. We offer reliable solutions to maximize the efficiency and performance of our clients’ machines or factory. Wide range of circuit switching, circuit and load protection, motor control products, push buttons, smart sensors and signaling devices is extended into additional dimension by adding plentiful range of industrial safety components.
Human Machine Interface
Visualization and HMI solutions help our clients address their productivity, innovation, and globalization needs. Rockwell Automation portfolio provides a consistent look and feel for electronic operator interface terminals, distributed client/server HMI, and information software. Programming tools and advanced software applications include remote access and data analysis to accelerate development and improve efficiency. In addition to legendary robust operator terminals, industrial computers and monitors we offer industry leading HMI software solutions that may be tailored to individual machines or to complex plant-wide operations. The ThinManager® is latest addition to the offering, bringing the air of new-age XaaS solutions. It is practically a thin client for any required plant-floor HMI. The benefit of the solution is that it is a centrally managed and hardware-agnostic solution that can be deployed, migrated, upgraded, recovered, you-name-it, in a matter of minutes.
Drives
Allen-Bradley® PowerFlex® variable frequency drives and Kinetix® servo drives offer solutions from simple machine control, high-speed positioning to demanding medium voltage control. These flexible portfolios deliver solutions to keep you connected to your operations and help you to be more productive.
- PowerFlex low voltage VFDs offer a broad selection of features and capabilities to match your application needs. Their power range is from 0.25...3000 Hp/0.2...2200 kW; global voltage range is from 100...690V. They support induction and permanent magnet motor types and include all latest communications and safety features.
- PowerFlex medium voltage VFDs provide efficient motor control to meet the needs of demanding applications in MW power ranges. The input voltage ranges are from 2.3-10kV, with a motor current up to 720A. In order to maintain adherence to the strictest standards the MV PowerFlex drives provide safety and arc resistance features in addition to rich communication capabilities.
- PowerFlex DC drives offer flexible and cost-effective DC control solutions providing the power range from 1.5...1400 Hp/1.2...1044kW, and global voltage range from 200...690V. The DC drives include specialized torque control for lifting applications
- Kinetix servo drive solutions are designed to simplify machine design while improving system performance. The portfolio starts with compact single-axis drives and goes up to high-performance multi-axis servo drive systems. They are tightly matched with compatible range of servo motors suitable for any application one can imagine.
By default, all PowerFlex drives, LV, MV and servo, provide seamless integration into the Logix control system.
THE CONNECTED ENTERPRISE
Smart manufacturing is the gateway to digital transformation. Connected smart devices open new windows of visibility into processes. Data and analytics enable better and faster decision making. Seamless connectivity spurs new collaboration. The Connected Enterprise is a genuine concept coming from Rockwell Automation visionaries that makes all this possible. It converges plant-level and enterprise networks, and securely connects people, processes, and technologies. Operational data is the lifeblood of digital manufacturing. By delivering the right information to the right worker at the right time, you empower workers to make better decisions. When our clients use smart machines that can diagnose or resolve issues on their own, they create smarter operations with less downtime.
We aim to support successful and secured transition that will ensure the maximum output from the digital manufacturing and eventually achieve improvement of productivity and profitability. Rockwell Automation, our partner in that undertaking, along with their strategic alliance partners Cisco, Microsoft, Panduit, and Endress+Hauser, offers solutions and services that give strong technological and strategic advantages to any industry, at any stage of the lifecycle.
Manufacturing Information Solutions
Information changes the face of manufacturing. Access to the metrics coming out of automation systems can help industry peers make critical improvements. With analytics that scale to production challenge, Rockwell Automation Information Solutions offer descriptive, diagnostic, predictive, and prescriptive analytics to turn data into your most valuable resource. Plant data has the power to inform every aspect of a business. Rockwell Software analytic applications can integrate with many business intelligence technologies beyond what is offered in the Rockwell Automation portfolio. Now every manufacturer can confidently tap production information and analyze big data no matter if the plant-wide automation standard is Rockwell Automation or any other Tier 1 vendor. Being that Rockwell Software FactoryTalk Manufacturing Intelligence and Analytics is a truly control system vendor agnostic solution, there is virtually no obstacle in getting just any valuable information from the plant floor up to the manufacturing management level in time and as-is.
Manufacturing Execution Solutions
Rockwell Automation manufacturing execution solutions are built on more than 100 years of production and control platform experience. Scalable offerings address the most critical needs for quick time to value and ease the path to smart manufacturing. We offer manufacturing execution systems (MES), industry suites and application solutions that provide workflows, business rules, and user experience configured on FactoryTalk® ProductionCentre® software. Production management is a key aspect of the RA MES solution. The FactoryTalk ProductionCentre software helps address the challenges that are associated with enforcing processes in manufacturing. It provides better synchronization of production activities and improves work-instruction delivery to personnel in increasingly complex operations. One can better manage the flow of materials from warehouses and suppliers. The FactoryTalk ProductionCentre software offers out-of-box integration with ERP to track order data, BOM, and recipe parameters. In addition to that the ProdutionCentre provides powerful tools for performance, quality management and regulatory compliance. It is a one-stop.
Industrial Internet of Things
The convergence of operational technology (OT) and information technology (IT) is raising questions within manufacturing and industrial organizations. Who and how will design and oversee the complex network infrastructures required to take advantage of the Industrial Internet of Things (IIoT)?
And what is the IIoT on the first place?
We perceive the Industrial Internet of Things (IIoT) as a subset of the broader IoT, where the people, processes, and things are primarily engaged in the production of physical goods and maintenance of physical assets. So where do we get the tools to handle this emerging potential?
Rockwell Automation division, Rockwell Software had been working around the clock to provide a product that will answer to those questions. They are introducing the Smart Connected Operations solution, natural extension of their concept of Connected Enterprise, as a future looking vision that describes what the factory or production line of the future will look like. It will involve Industrial Internet of Things (IIoT) enabled Manufacturing Operation Management applications integrated with IIoT enabled assets and IIoT enabled business systems.
ROBOT SYSTEMS
“Necessity is the mother of invention.” - Greek philosopher Plato’s statement was proven countless times. In essence: a need or problem encourages creative efforts to meet the need or solve the problem. That is why we firmly believe that introduction of robot systems into industrial processes is much more of the actual process need than a mere workforce replacement issue. Working with KUKA robots is like taking a completely new viewpoint. It is making us learn new skills and forcing us to change our methodologies.
We offer a portfolio of Allen-Bradley industrial control products that deliver proven and predictable performance over the full life of the product. We offer reliable solutions to maximize the efficiency and performance of our clients’ machines or factory. Wide range of circuit switching, circuit and load protection, motor control products, push buttons, smart sensors and signaling devices is extended into additional dimension by adding plentiful range of industrial safety components.
Industrial Robots
KUKA offers a comprehensive range of industrial robots:
- Six-axis robots in virtually all sizes with different payload capacities and reaches and a wide range of different variants
- HRC-capable lightweight robots for direct human-robot collaboration
- Heat- and dirt-resistant robots for extreme ambient conditions
- Industrial robots in cleanroom variants for strict hygiene requirements
- Small robots with waterproof equipment suitable for use in machine tools
- Press-to-press robots with enormous reaches for loading and unloading large parts in press-linking operations
- Palletizing robots for handling tasks of all kinds
- Welding robots designed for accuracy and utmost agility
- Shelf-mounted robots in all variants
- High-accuracy robots for utmost precision
Robot periphery
The robot periphery is a factor that must not be underestimated when considering the efficiency of your production processes. With end effectors, energy supply systems, linear units and positioners, you can considerably expand the functionality of KUKA robots. KUKA offers additional modules for all payload categories, for full automation and human-robot collaboration:
- End effectors - from power wrenches to grippers or suction cups: KUKA is sure to offer the right “fingers” for your robot.
- Robot energy supply systems - external dress packages supply the robot and application with the required energy. Available for robot models of all payload classes.
- Linear units - with KUKA linear units, you add a further axis to the robot, thereby considerably extending the work envelope of the robot.
- Positioners - KUKA offers a broad portfolio of standard positioners for payloads from 250 to 12,000 kilograms.
Linear kinematic systems
KUKA provides an extensive range of versatile linear kinematic systems that can be adapted to your specific automation requirements. Various travel lengths and additional options allow you to interlink work sequences between machines and systems efficiently. By using linear kinematic systems from KUKA, you can achieve top process efficiency when automatically interlinking work sequences between injection molding machines, machine tools and further processing systems. The linear kinematic systems are therefore ideal for tasks such as automatic loading and unloading, turning and transferring. By combining standard modules, you can also implement Cartesian gantry solutions and two-axis loading and unloading robots. KUKA linear kinematic systems offer great versatility: payload capacities from 16 to 600 kilograms, repeatability of plus/minus 0.1 to 0.3 millimeters and various travel lengths are available. The systems may be adapted to match specific requirements by installing rotational external axes and various gripper devices.
- INDUSTRIAL AUTOMATION AND CONTROL
- THE CONNECTED ENTERPRISE
- ROBOT SYSTEMS
INDUSTRIAL AUTOMATION AND CONTROL
The rapid evolution of technology in industrial automation systems requires tighter integration between devices on the plant floor and the rest of the enterprise. This involves a secure network infrastructure, smart devices for efficient data collection, and the ability to turn data into actionable information.
The integration of control and information across the enterprise enables our customers to optimize their operations by connecting the plant, site, facility, and people. We deliver industrial automation and control through our control systems, motor control, and smart devices portfolios. The combination of these three platforms are architected and designed to help you build the most efficient industrial automation system to meet your needs.
Integrated Architecture
Integrated control systems facilitate smart manufacturing for your industrial automation solution. Rockwell Automation Integrated Architecture® system enables the deployment of an industrial control system individually at a machine- or line-level to solve specific needs. It can then be scaled across multiple lines or plants to achieve enterprise-wide business objectives. It helps converge control and information to deliver the connected enterprise with smarter technology, enhanced productivity, and a more secure environment. The Integrated Architecture portfolio includes ControlLogix control, FactoryTalk visualization, Kinetix motion, and Cisco-based Stratix networking solutions. Our everyday experience from various projects is that this technology has the power to improve plant processes at every stage of manufacturing, from design and installation to operation and maintenance.
Intelligent Motor Control
Efficient motors drive performance and the impact of motor failure can be significant. With intelligent motor control devices, our clients can improve productivity and help avoid motor failures with an integrated, data-driven approach. The Allen-Bradley portfolios of PowerFlex® variable frequency drives, Kinetix® servo drives and CENTERLINE® motor control centers offer solutions for any application with requirements for speed, torque or positioning control. To gain further advantages we ensure that they are combined with the Logix control architecture to reduce the design time, keep clients connected to the operations and help them to be more productive.
Universal Automation System Designer
The Rockwell Automation Studio 5000® environment combines engineering and design elements into one standard framework that enables optimized productivity and reduced commissioning time. The Studio 5000 is a universal system designer that covers of stages of one complex project: Architect, Logix Designer, View Designer, Application Code Manager and Logix Emulate.
https://www.rockwellautomation.com/en-us/products/software/factorytalk/designsuite/studio-5000.html
Industrial Networks
For plants to become information driven, they need a strong foundation consisting of one industrial network architecture. It is crucial to send data to the right place, at the right time, and in the right context. A network infrastructure that is built on standard Ethernet and IP enables the flow of data across your global enterprise. Industry adoption of EtherNet/IP™ for control and information enables the convergence of industrial and enterprise networks. To support and accelerate this network convergence, Rockwell Automation has collaborated with Cisco and other partners to provide design guidance and best practices to deploy scalable, robust, secure, safe, and future-ready industrial network architectures. They have addressed topics relevant to both operations technology (OT) and information technology (IT) professionals. Rockwell Automation offer of industrial network products consists of a wide variety of industrial network solutions including switches, routers, physical media, and connecting products.
Industrial Automation Components
We offer a portfolio of Allen-Bradley industrial control products that deliver proven and predictable performance over the full life of the product. We offer reliable solutions to maximize the efficiency and performance of our clients’ machines or factory. Wide range of circuit switching, circuit and load protection, motor control products, push buttons, smart sensors and signaling devices is extended into additional dimension by adding plentiful range of industrial safety components.
Human Machine Interface
Visualization and HMI solutions help our clients address their productivity, innovation, and globalization needs. Rockwell Automation portfolio provides a consistent look and feel for electronic operator interface terminals, distributed client/server HMI, and information software. Programming tools and advanced software applications include remote access and data analysis to accelerate development and improve efficiency. In addition to legendary robust operator terminals, industrial computers and monitors we offer industry leading HMI software solutions that may be tailored to individual machines or to complex plant-wide operations. The ThinManager® is latest addition to the offering, bringing the air of new-age XaaS solutions. It is practically a thin client for any required plant-floor HMI. The benefit of the solution is that it is a centrally managed and hardware-agnostic solution that can be deployed, migrated, upgraded, recovered, you-name-it, in a matter of minutes.
Drives
Allen-Bradley® PowerFlex® variable frequency drives and Kinetix® servo drives offer solutions from simple machine control, high-speed positioning to demanding medium voltage control. These flexible portfolios deliver solutions to keep you connected to your operations and help you to be more productive.
- PowerFlex low voltage VFDs offer a broad selection of features and capabilities to match your application needs. Their power range is from 0.25...3000 Hp/0.2...2200 kW; global voltage range is from 100...690V. They support induction and permanent magnet motor types and include all latest communications and safety features.
- PowerFlex medium voltage VFDs provide efficient motor control to meet the needs of demanding applications in MW power ranges. The input voltage ranges are from 2.3-10kV, with a motor current up to 720A. In order to maintain adherence to the strictest standards the MV PowerFlex drives provide safety and arc resistance features in addition to rich communication capabilities.
- PowerFlex DC drives offer flexible and cost-effective DC control solutions providing the power range from 1.5...1400 Hp/1.2...1044kW, and global voltage range from 200...690V. The DC drives include specialized torque control for lifting applications
- Kinetix servo drive solutions are designed to simplify machine design while improving system performance. The portfolio starts with compact single-axis drives and goes up to high-performance multi-axis servo drive systems. They are tightly matched with compatible range of servo motors suitable for any application one can imagine.
By default, all PowerFlex drives, LV, MV and servo, provide seamless integration into the Logix control system.
THE CONNECTED ENTERPRISE
Smart manufacturing is the gateway to digital transformation. Connected smart devices open new windows of visibility into processes. Data and analytics enable better and faster decision making. Seamless connectivity spurs new collaboration. The Connected Enterprise is a genuine concept coming from Rockwell Automation visionaries that makes all this possible. It converges plant-level and enterprise networks, and securely connects people, processes, and technologies. Operational data is the lifeblood of digital manufacturing. By delivering the right information to the right worker at the right time, you empower workers to make better decisions. When our clients use smart machines that can diagnose or resolve issues on their own, they create smarter operations with less downtime.
We aim to support successful and secured transition that will ensure the maximum output from the digital manufacturing and eventually achieve improvement of productivity and profitability. Rockwell Automation, our partner in that undertaking, along with their strategic alliance partners Cisco, Microsoft, Panduit, and Endress+Hauser, offers solutions and services that give strong technological and strategic advantages to any industry, at any stage of the lifecycle.
Manufacturing Information Solutions
Information changes the face of manufacturing. Access to the metrics coming out of automation systems can help industry peers make critical improvements. With analytics that scale to production challenge, Rockwell Automation Information Solutions offer descriptive, diagnostic, predictive, and prescriptive analytics to turn data into your most valuable resource. Plant data has the power to inform every aspect of a business. Rockwell Software analytic applications can integrate with many business intelligence technologies beyond what is offered in the Rockwell Automation portfolio. Now every manufacturer can confidently tap production information and analyze big data no matter if the plant-wide automation standard is Rockwell Automation or any other Tier 1 vendor. Being that Rockwell Software FactoryTalk Manufacturing Intelligence and Analytics is a truly control system vendor agnostic solution, there is virtually no obstacle in getting just any valuable information from the plant floor up to the manufacturing management level in time and as-is.
Manufacturing Execution Solutions
Rockwell Automation manufacturing execution solutions are built on more than 100 years of production and control platform experience. Scalable offerings address the most critical needs for quick time to value and ease the path to smart manufacturing. We offer manufacturing execution systems (MES), industry suites and application solutions that provide workflows, business rules, and user experience configured on FactoryTalk® ProductionCentre® software. Production management is a key aspect of the RA MES solution. The FactoryTalk ProductionCentre software helps address the challenges that are associated with enforcing processes in manufacturing. It provides better synchronization of production activities and improves work-instruction delivery to personnel in increasingly complex operations. One can better manage the flow of materials from warehouses and suppliers. The FactoryTalk ProductionCentre software offers out-of-box integration with ERP to track order data, BOM, and recipe parameters. In addition to that the ProdutionCentre provides powerful tools for performance, quality management and regulatory compliance. It is a one-stop.
Industrial Internet of Things
The convergence of operational technology (OT) and information technology (IT) is raising questions within manufacturing and industrial organizations. Who and how will design and oversee the complex network infrastructures required to take advantage of the Industrial Internet of Things (IIoT)?
And what is the IIoT on the first place?
We perceive the Industrial Internet of Things (IIoT) as a subset of the broader IoT, where the people, processes, and things are primarily engaged in the production of physical goods and maintenance of physical assets. So where do we get the tools to handle this emerging potential?
Rockwell Automation division, Rockwell Software had been working around the clock to provide a product that will answer to those questions. They are introducing the Smart Connected Operations solution, natural extension of their concept of Connected Enterprise, as a future looking vision that describes what the factory or production line of the future will look like. It will involve Industrial Internet of Things (IIoT) enabled Manufacturing Operation Management applications integrated with IIoT enabled assets and IIoT enabled business systems.
ROBOT SYSTEMS
“Necessity is the mother of invention.” - Greek philosopher Plato’s statement was proven countless times. In essence: a need or problem encourages creative efforts to meet the need or solve the problem. That is why we firmly believe that introduction of robot systems into industrial processes is much more of the actual process need than a mere workforce replacement issue. Working with KUKA robots is like taking a completely new viewpoint. It is making us learn new skills and forcing us to change our methodologies.
We offer a portfolio of Allen-Bradley industrial control products that deliver proven and predictable performance over the full life of the product. We offer reliable solutions to maximize the efficiency and performance of our clients’ machines or factory. Wide range of circuit switching, circuit and load protection, motor control products, push buttons, smart sensors and signaling devices is extended into additional dimension by adding plentiful range of industrial safety components.
Industrial Robots
KUKA offers a comprehensive range of industrial robots:
- Six-axis robots in virtually all sizes with different payload capacities and reaches and a wide range of different variants
- HRC-capable lightweight robots for direct human-robot collaboration
- Heat- and dirt-resistant robots for extreme ambient conditions
- Industrial robots in cleanroom variants for strict hygiene requirements
- Small robots with waterproof equipment suitable for use in machine tools
- Press-to-press robots with enormous reaches for loading and unloading large parts in press-linking operations
- Palletizing robots for handling tasks of all kinds
- Welding robots designed for accuracy and utmost agility
- Shelf-mounted robots in all variants
- High-accuracy robots for utmost precision
Robot periphery
The robot periphery is a factor that must not be underestimated when considering the efficiency of your production processes. With end effectors, energy supply systems, linear units and positioners, you can considerably expand the functionality of KUKA robots. KUKA offers additional modules for all payload categories, for full automation and human-robot collaboration:
- End effectors - from power wrenches to grippers or suction cups: KUKA is sure to offer the right “fingers” for your robot.
- Robot energy supply systems - external dress packages supply the robot and application with the required energy. Available for robot models of all payload classes.
- Linear units - with KUKA linear units, you add a further axis to the robot, thereby considerably extending the work envelope of the robot.
- Positioners - KUKA offers a broad portfolio of standard positioners for payloads from 250 to 12,000 kilograms.
Linear kinematic systems
KUKA provides an extensive range of versatile linear kinematic systems that can be adapted to your specific automation requirements. Various travel lengths and additional options allow you to interlink work sequences between machines and systems efficiently. By using linear kinematic systems from KUKA, you can achieve top process efficiency when automatically interlinking work sequences between injection molding machines, machine tools and further processing systems. The linear kinematic systems are therefore ideal for tasks such as automatic loading and unloading, turning and transferring. By combining standard modules, you can also implement Cartesian gantry solutions and two-axis loading and unloading robots. KUKA linear kinematic systems offer great versatility: payload capacities from 16 to 600 kilograms, repeatability of plus/minus 0.1 to 0.3 millimeters and various travel lengths are available. The systems may be adapted to match specific requirements by installing rotational external axes and various gripper devices.